NanoAndMore GmbH does not ship to your country
Non-Contact / Standard Tapping Mode AFM Probes
Non-contact or tapping mode AFM imaging of hard material samples are probably the most commonly used AFM modes. In these dynamic modes, the AFM cantilever is forced to oscillate at or close to its resonance frequency by an actuator integrated into the AFM probe mount of the AFM – typically a small piezo-ceramic shaker.
When approaching the sample surface, the AFM cantilever oscillation is damped. The amplitude of oscillation drops, the phase with respect to the driving signal changes and the resonance frequency decreases due to the damping. Usually, either the amplitude signal or the phase signal change is used for the feedback loop that keeps the AFM probe-sample-distance constant by adjusting the z-position of the AFM probe.
The output signal of the feedback loop moving the z-position is a direct measure of the sample height at the current AFM tip location. The raw signal, which is typically a voltage, is converted into a length scale on basis of a calibration table for the nonlinear z-movement of the AFM head. Alternatively, in modern AFM systems, the z-movement of the AFM head is measured by a separate sensor in the AFM head to improve accuracy. This concept is called ‘closed-loop’ whereas the use conversion of feedback output signals is called ‘open-loop’.
The difference between non-contact and tapping mode AFM (sometimes called intermittent mode) is the interaction with the sample surface. While the AFM tip does not touch the surface in non-contact mode it does get in contact with the surface at the peak of its oscillation in tapping mode AFM. More precisely, the AFM tip stays in the regime of attractive forces (basically Van-der-Vaals-Forces) during the complete oscillation cycle for non-contact AFM mode whereas the AFM tip dips into the repulsive force regime of a contact between AFM tip and sample in tapping mode. Tapping mode AFM uses larger amplitudes in the regime of several tens of nanometers while non-contact mode AFM tip oscillations are typically less than 10nm.
A common problem of these measurement modes is that the AFM tip tends to stick to the surface if the attractive forces of the AFM tip-sample interaction are larger than the retraction forces during oscillation. Therefore, a minimum force constant is required for AFM probes suitable for these modes. In many cases this so-called ‘snap-in’ effect is caused by adhesion or capillary forces of surface contaminations and liquid films at the sample surface.
In practice, the use of AFM probes with force constants of a few tens of N/m have shown to be a good compromise between stability of operation and limited forces for non-contact or tapping mode at hard surfaces as silicon or graphite or other similarly stiff materials. Higher force constants increase the risk of AFM tip or sample damages unless the oscillation amplitude is not reduced significantly to a level which is difficult to detect by the AFM deflection detection system.
Large resonance frequencies are desirable because they allow a fast scanning of surfaces without losing information. Nevertheless, AFM probes for standard non-contact and tapping mode AFM do not have the highest possible resonance frequency. The reason for that is that such high resonance frequencies require special AFM cantilever geometries, deflection detection systems adjusted to theses geometries and, last but not least, very fast AFM feedback mechanisms that are not yet implemented in most AFM systems. Therefore, AFM probes for fast scanning are listed in a separate category on our website - Ultra High Frequency, Ultra Short AFM Cantilevers.
Another AFM probe feature that is very important for their application in non-contact or tapping mode AFM in air is the AFM tip height. The damping of AFM cantilevers far away from any sample is usually dominated by air damping. When approaching the sample surface, damping is increased significantly long before the AFM tip-sample interactions are visible – microns away from the AFM tip-sample contact. This damping increase is caused by the air between AFM cantilever and surface that gets squeezed during oscillation resulting into the so-called ‘squeezed air-film damping’ effect. The setpoint of the feedback loop must be chosen in a way that the approach does not stop at this point but penetrates through the ‘air-film’. Obviously, sensitivity of measurement decreases due to this shift of setpoint. An AFM tip height of more than 10µm is required for reducing this effect drastically. All AFM probes listed as suitable for non-contact or tapping mode AFM meet this requirement.
Moreover, most AFM probes offered here are featuring a trapezoidal cross-section of the AFM cantilever which further decreases the squeezed air-film effect while keeping the necessary force constant. A side-effect of this trapezoidal cross-section is that the reflective area of the AFM cantilever at the detector side is larger (compared to AFM cantilevers with a rectangular cross section with otherwise similar AFM cantilever values) which increases the reflected laser signal (sum signal) of a beam deflection AFM.
A variety of AFM cantilever shapes with different mechanical properties as well as different AFM tip shapes are provided by all manufacturers of AFM probes. All AFM probes are made from single crystalline silicon. An optional coating with Aluminum or Gold on the detector side of the AFM cantilever enhances the reflectivity. The use of AFM probes with a frequency of about 300kHz is recommended unless restrictions of the AFM tool or the particular application does not require different AFM cantilever geometries or softer AFM cantilevers. Reflection coating improves signal-to-noise ratio but causes thermal drifts in case of varying temperatures during measurement. Nevertheless, it is recommended for applications performed without large variations of temperature.
All AFM probes in this category are widely used and have proven their performance in many cases and scientific publications. In many AFM laboratories all over the world, these AFM probes are the first choice for the most common AFM surface imaging applications.
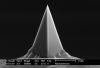
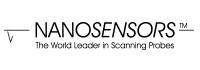
Tip Shape: Standard
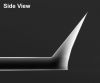
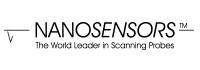
Tip Shape: Visible
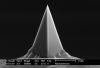
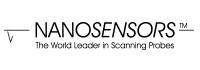
Tip Shape: Standard
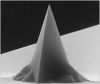
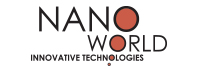
Tip Shape: Standard
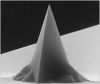
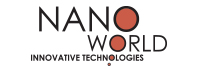
Standard Tapping Mode AFM Probe
Tip Shape: Standard
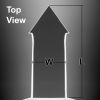
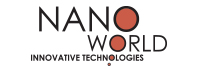
Tip Shape: Arrow
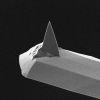
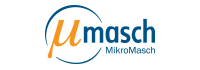
Tip Shape: Rotated
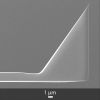
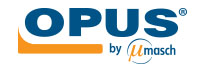
Tip Shape: Optimized Positioning
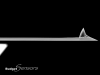
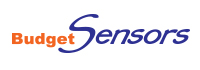
Tip Shape: Rotated
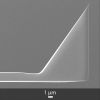
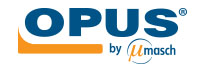
Tip Shape: Optimized Positioning
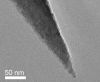
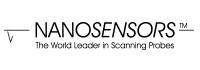
Tip Shape: Standard
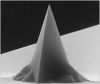
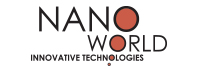
Tip Shape: Standard
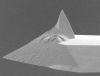
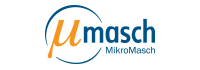
Tip Shape: Rotated
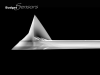
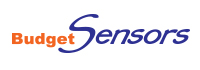
Tip Shape: Rotated
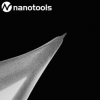
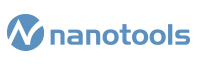
Tip Shape: Cone Shaped,EBD
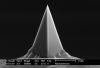
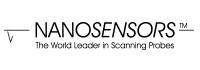
Tip Shape: Standard
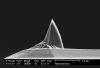
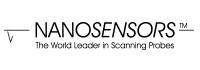
Tip Shape: Rotated
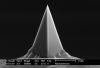
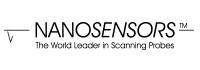
Tip Shape: Standard
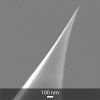
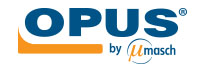
Tip Shape: Optimized Positioning
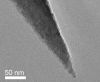
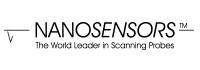
Tip Shape: Standard